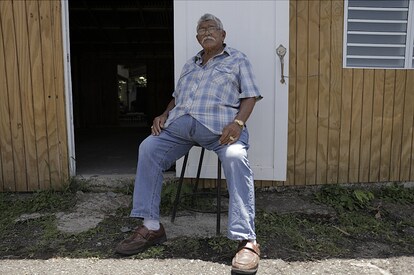
Strong winds can create pressure on the building envelope, potentially causing the roofing system to lift. However, conducting roof uplift testing on roofing systems can help predict how a roof will perform when subjected to strong winds.
What Is Wind Uplift?
Wind can exert three types of force on a structure—shear load, lateral load, and uplift load. Although all three load forces can damage a building, the uplift load most intensely affects the roofing system.
The NRCA defines wind uplift load as "The force caused by the deflection of wind at roof edges, roof peaks or obstructions causing a drop in air pressure immediately above the roof surface." However, the same lifting effect that enables airplanes to fly can be devastating for a roofing system. When wind flows under a roof, it pushes upward, elevating the roof membrane. As wind flows over the roof, it pulls the roofing system upward.
Understanding local wind zones and building codes will help determine the requirements needed for the roofing system to best protect the building. This is typically handled by an architect or roofing design professional. James R. Kirby, AIA, GAF building and roof science architect, writes in an article for the American Institute of Architects that the architect's responsibility is to provide wind pressures, whereas the manufacturer must determine the wind uplift capacity of the roofing system.
What Are Roof Uplift Testing Methods?
Professionals use two methods to perform wind uplift testing.
In-Facility Testing
Most manufacturers rely on unbiased, third-party testing labs that are accredited to determine wind uplift resistance of a roofing system. A few of the more well-known facilities include FM Approvals, Underwriters Laboratory, and Intertek. There are a number of industry-accepted testing standards for indoor test facilities, including ASCE-7, ANSI/SPRI, and ANSI/FM 4474.
During testing, these companies subject roof deck mockups (at least 10' x 10') to winds and conditions that mimic various wind speeds with increasing levels of pressure. The roof earns its certification based on its maximum wind performance rating—the level of wind speed that it was able to withstand without failure.
Although lab certifications are important, the building's location, use, occupancy, and wind zone can create unique conditions that may be difficult to replicate in a lab environment.
Field Testing
Roof uplift testing in the field involves placing a dome-like structure measuring 5' x 5' onto the roof surface that subjects the roof to negative pressure forces. The roofing system is observed at different levels of pressure to the point where the system is considered on the brink of failure. This point can vary depending on the criteria being followed—either specified by ASTM or FM Global.
The National Roofing Contractors Association (NRCA) has maintained that field testing is "inappropriate for use" to measure the quality of a membrane roof installation. The organization recommends that contractors avoid jobs that specify field testing as a condition of acceptable installation. A roofing system's ability to pass wind uplift testing relies on many more factors than just the contractor's installation. It's in the contractor's best interest to clearly spell out expectations; the NRCA offers suggested language to use in the project contract.
The NRCA says the most reliable way to determine the quality of a newly installed roof system is by having a "knowledgeable roofing professional" observe the installation. The International Institute of Building Envelope Consultants (IIBEC) agrees, stating in a technical advisory that they recommend observation by an IIBEC Registered Roof Consultant or Registered Roof Observer: "continuous installation monitoring allows for observing the entire assembly process and for corrective action of observed deficiencies as the roof is being installed."
Turn to the Experts
With the number of variables that go into ensuring a roofing system's performance during wind events, it can be challenging to determine the right system and installation method. Not every roofing project will have an architect or design professional behind the specification. In those cases, GAF is here to provide guidance on roofing system options where wind uplift pressures are an important consideration.