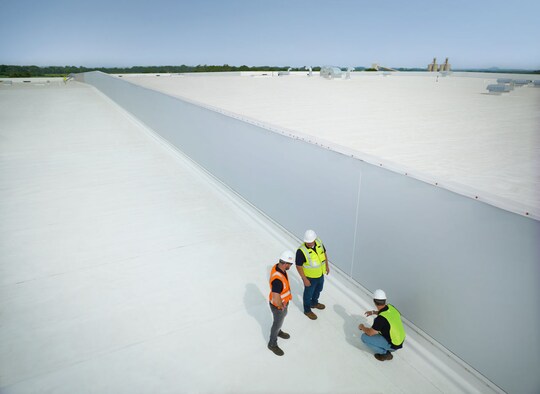
Looking for the best roofing materials for your outdoor office, shed, or garage roof? It's not just about curb appeal—although looks are important.
Learning about the materials to consider for your roof pitch can help you reduce the risk of roof leaks. You can also benefit by knowing when you need roof ventilation or drip edging, when to consider insulation, and how to calculate roof materials costs. Here are the key details to understand.
The Importance of Aesthetics
Visual consistency is crucial when it comes to curb appeal. You want garage roof materials that flow with your home's architectural style, building materials, and color palette. For example, if you have an ornate Tudor-style home with wood-look architectural asphalt shingles, choosing a green metal roof for your garage could be visually jarring.
When it comes to winning home aesthetics, consider:
- Your garage's architectural style
- Which materials will complement your home architecture and colors
- How the new garage roof will look from the street (a.k.a. its curb appeal)
Accounting for Roof Slope
How steep or flat is your roof? Knowing can save you time and money because different roof slopes call for different roofing materials. To calculate your garage roof slope, determine how many inches your roof rises vertically for every 12 inches it extends horizontally. For example, if your roof's vertical rise is 6 inches, your roof pitch is 6:12.
Materials for High-Pitch Roofs
Generally, any roof pitch over 3:12 is considered a high-pitch or steep-slope roof. Steeper pitches tend to allow water, snow, and debris to slough off more easily than lower-slope roofs. Here are some materials the International Building Code (IBC) approves for high-pitch roofs:
Metal Roof Panels or Shingles
Typically having high fire-resistance ratings and offered in a range of colors, metal roofs are sleek and simple. They can be made from galvanized steel, aluminum, copper, zinc, and stainless steel. This material is long-lasting but is high cost.
Clay or Concrete Tiles
These tiles are commonly associated with Mediterranean or Southwestern-style architecture. Tiles provide great wind, impact, and high fire resistance ratings but are a pricier option. You also need to verify your structure can support this material's weight.
Wood Shingles
Wood shingles are aesthetically pleasing—and often seen in New England-style and Shingle Style homes—but may have lower fire resistance ratings than other options. An alternative to wood shingles are asphalt shingles with a wood shake-look, like GAF Timberline® NS Shingles.
Slate Shingles
Often seen on Northeastern homes and in high-end modern design, slate shingles can provide high fire resistance ratings, durability, and offer good insulation. But slate roofs are heavy and have a high cost.
Asphalt Shingles
Versatile, affordable, and attractive, asphalt shingles are the most popular roofing material in the US. Offered in a range of prices, styles, and roof shingle colors, asphalt shingles provide high fire resistance ratings and are reliable as well as low maintenance. It's important to note that the IBC has special underlayment requirements for roof pitches of 3:12 or less.
Always read the material manufacturer's requirements and adhere to installation instructions. Additionally, always check local building codes before selecting your roof materials.
Materials for Low-Slope and Flat Roofs
Flat and low-slope roofs can range in pitch from ¼:12 to 3:12. Flat roofs aren't completely flat because some slope is required for water runoff. Roofs with lower slopes can be more prone to water and moisture pooling than steep-slope roofs, so adhere to installation requirements to help prevent leaks. IBC-approved materials for lower-slope roofs include:
Self-Adhesive Membranes
A streamlined and versatile option, these watertight roof covers help protect against the inevitable water pooling that occurs on lower-slope roofs. Options like the GAF LIBERTY™ SBS Self-Adhering Roofing System offer attractive and durable protection. For example, the granule-surfaced GAF LIBERTY™ System has a quick and clean installation process, and comes in seven colors that complement GAF shingle colors.
Asphalt Shingles
The IBC approves the use of asphalt shingles on roofs with a pitch under 2:12, but a special underlayment installation is required to meet the IBC code. Work with local building codes, manufacturer requirements, and professional guidance to ensure proper use and installation of shingles on lower-slope roofs.
Roll Roofing
A good option for smaller residential roof projects, quick-install products like GAF Mineral Guard Residential Roll Roofing (for pitches 2:12 or lesser) provide roof protection and convenience.
How Roof Ventilation Helps Protect Your Investment
Proper roof ventilation can help protect your garage or shed interior by allowing damaging heat and moisture to escape. Check out the most common attic ventilation solutions by roof style.
Use the handy GAF Attic Ventilation Calculator to get started.
Why Climate Matters for Your Roofing Materials
Consider your regional climate before selecting roofing materials. Keep in mind average temperatures, average rain and snowfall, average wind speeds throughout the year, amount of sunshine, and frequency and type of natural disasters like hurricanes.
For example, in high-wind and storm regions, a durable asphalt shingle like Timberline HDZ® (eligible for a 15-year WindProven Limited Wind Warranty** with no maximum wind speed limitation when installed with required combination of four qualifying GAF accesssories—or up to 110 mph wind coverage without special installation) is a solid choice.
The Role of Drip Edge
Roofing materials like drip edge and flashing help prolong the life of your building. Without drip edge, your garage roof is more prone to water damage, pest infestations, and ice dams. Roof flashing keeps water from sneaking into roof joints if you have a larger project. Remember these important elements when selecting your garage roof shingles.
When to Install Insulation
Roof insulation could save you money on energy bills* if you'll be heating or cooling your garage or shed. Plus, insulation helps keep internal temperatures comfortable, which is important if you're using the building as a workspace.
The Cost of Roof Garage Materials
Roof materials are typically priced by the square. In roofing, one square equals 10 by 10 feet, or 100 square feet. Learn how to measure a roofing square to help determine your project size and cost. Keep in mind that a roof for a smaller building roof will be less expensive than the average cost of a new roof for your whole home.
Follow these steps to help estimate cost:
- Identify the best materials for your project based on the roof slope, aesthetics, etc.
- Determine the amount and different types of materials you'll need based on your roof size. Don't forget ventilation products if needed!
- Decide if you'll need professional help to safely and properly install your roof; if so, account for area labor costs.
Ready to get started on your new garage or shed roof today? Get reliable help from a GAF-Certified Roofing Contractor.